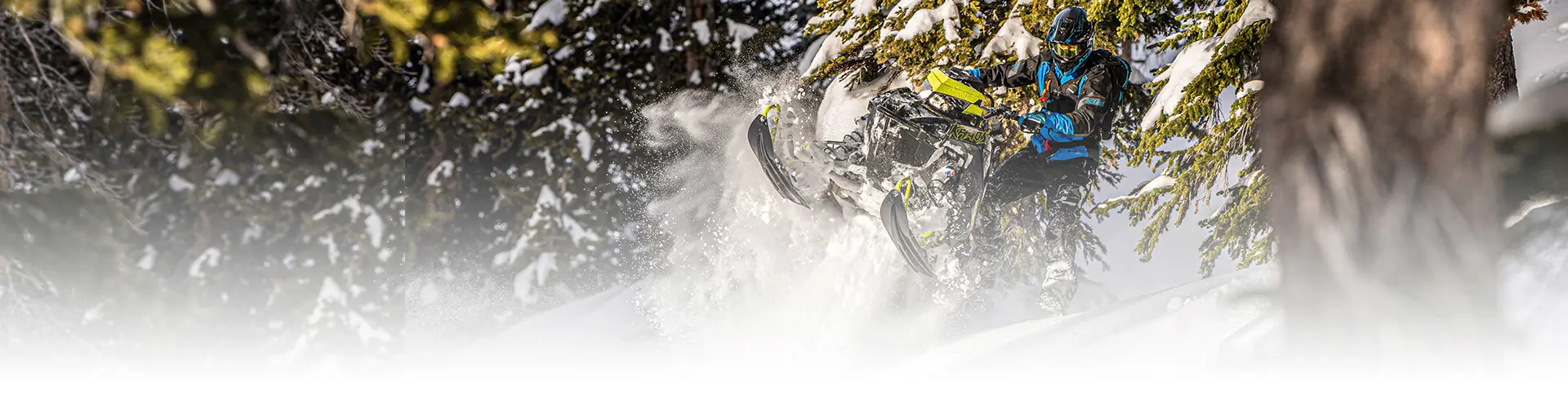
Building Boost Part 1: The Beginning
Just 10 miles south of the Canadian border, it was a hot and humid day in the summer of 2018 in Roseau, Minnesota. Assembly Line C at the Polaris Factory was buzzing along with brand new 2019 snowmobiles rolling down the line, ready to go to dealers all over the world. The all-new Patriot 850 had just been released, and thousands of customers were anxiously awaiting their SnowCheck snowmobile. Just a few steps away from the line, Jim Buchwitz & Darren Hedlund sat at the table outside Dyno Cell #6. Inside on the dyno stand was a project they both knew well – 10 years of hard work, struggle, and pioneering technology.
The turbocharged Patriot 850 engine in the dyno room was the latest of countless iterations built, completely unique from anything else on the market. The exhaust had just failed, a weld had cracked in the hand built prototype tuned pipe. The engineers, however, saw something they liked: the engine combustion and pressure into the turbo stabilized to a level they hadn’t seen before. The longtime members of the Polaris Engineering team headed back in to inspect the damage, curious what had sparked the improvement. Unknown to them at the time, the learning from that failure would lead to a stack of patents around an all-new, industry leading technology called Patriot Boost.
“It was never about just building a turbo. It was about building the next level of performance." — Darren Hedlund, Powertrain Development Specialist
Author's Note: “As our team began working on the launch of the 2022 Patriot Boost, it became clear there was a story. Beyond the specs, features, and benefits, there was a story of a passionate group of people stepping up to the challenge and delivering the new standard in snowmobile performance. It is a story that deserves to be told.” — Nels Eide, Snowmobile Product Marketing
An Inside Look at Building The World's Most Powerful OEM 2-Stroke Turbo
The idea of using forced induction to increase power certainly isn’t new, with automotive turbocharging coming on to the scene in the 1980s. Powersports has seen the turbocharging boom in recent years, with 4-stroke turbo snowmobiles and side by sides. The formula is rather simple – add compressed air, some extra fuel and more power seemingly appears like magic. With 2-stroke engines, however, the turbo solution isn’t nearly as straightforward.

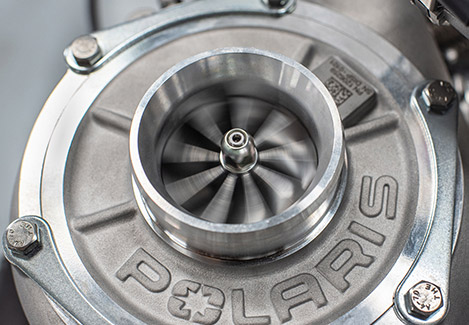
The Polaris team knew that mountain riders were always looking for more power, and that some had turned to aftermarket turbochargers. The early 2000s saw the entry of the first aftermarket turbo kits for 2-stroke snowmobile engines. The Polaris team had ridden them, and the power benefit was clear – especially in the growing mountain segment. As a naturally aspirated engine climbs in elevation, there is nothing to combat the loss in available oxygen and thus power – roughly 3% for every thousand feet of elevation. Forced induction from a turbocharger can compress the thinner air, maintaining sea level power numbers higher up the mountain. In the winter of 2006, a few engineers built a couple sleds with aftermarket turbos and began testing, tweaking, and investigating. They knew that customers wanted a turbo 2-stroke with the quality, reliability and performance a production version could offer, they just had to figure out how to build it. The turbo project had begun.

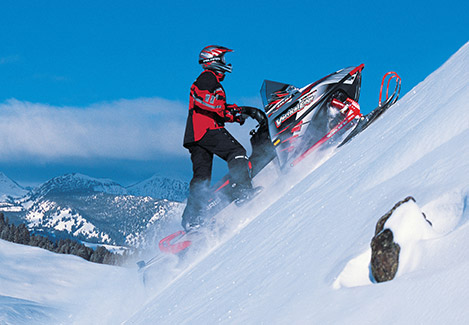
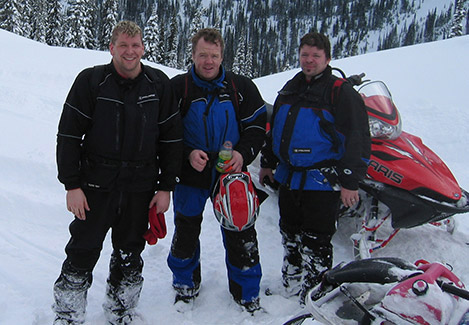
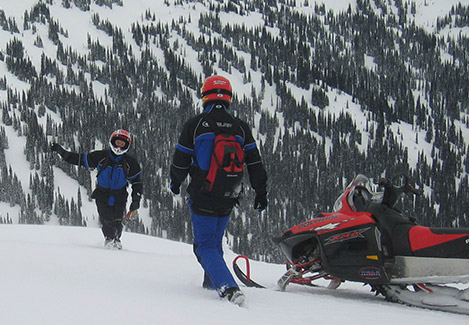
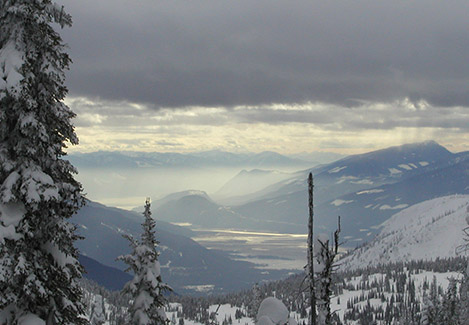
After a few years of initial work and making their case, the engineering team received funding from the greater Polaris corporation: conduct a technology investigation into a production turbocharged 2-stroke engine. Was it possible, and if so, what was needed to get it done. Although the side-by-side segments had taken over the largest volume of business at Polaris from ATV, leaving snowmobiles third, there was a lot of heart for snowmobiles and this type of turbo project. Polaris had been nothing but a snowmobile manufacturer for over 30 years, and that passion runs deep to this day.
Initial investigations revealed that while the aftermarket kits with Polaris engines indeed made more power, they came up short in a few key areas: emissions, sound, driveability, and combustion stability.
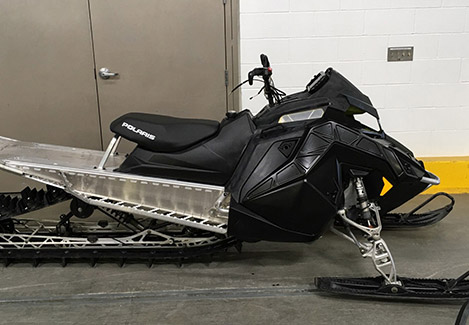
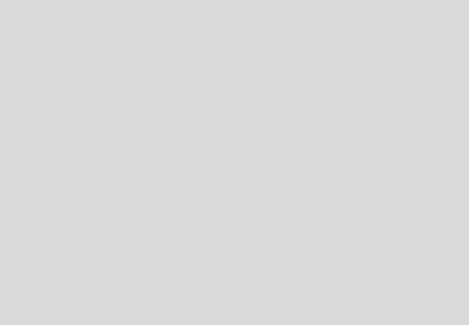
The first is rather straight forward – manufacturers are required to comply with emissions standards in the countries in which they sell snowmobiles. Aftermarket companies don’t have these rules and regulations, allowing them to take shortcuts simply not available to the manufacturers. The second, combustion stability, is much more difficult.
Whenever someone states how much power their highly modified forced induction engine makes, a common follow-up question is asked: ‘What fuel are you running?’. The question has merit: more power requires more boost, and high-octane specialty fuels are much better suited to high boost applications. Their cool-burning properties and knock resistance maintain stable combustion, all positives when it comes to boosted power. In a production setting, however, there is only one answer to that question – 91 octane pump gas. These exotic, expense fuels that the aftermarket turbo kits used aren’t available in an OEM setting, plain and simple. The engine combustion would have to be stable and powerful on pump gas.
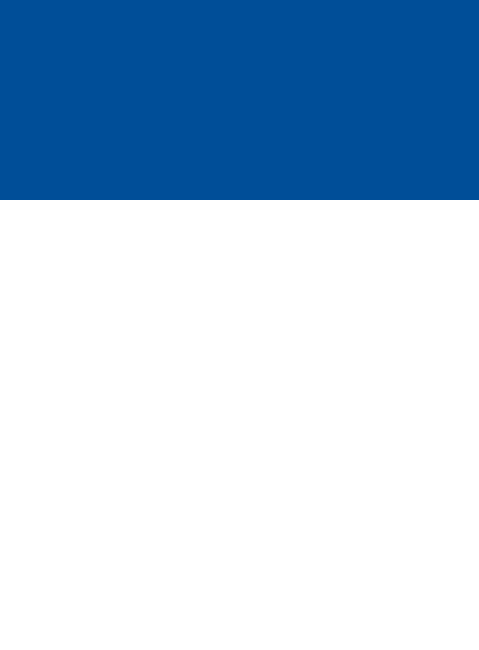
However great the challenge, the game changing technology and the potential it had to take mountain riders and their sleds to the next level was deemed crucial. After all – Polaris is made up of dedicated snowmobilers who love a challenge. In 2012, a small subset of the powertrain team got to work on a project code-named Medusa. The namesake of the program is the mythological sea-monster Medusa, with snakes in place of hair and a gaze that would turn people to stone. Not exactly a friendly image, but one that was certainly appropriately named. The project wouldn’t be easy, with challenges around seemingly each turn as the team worked toward something no one else had been able to do: build a stable, high performance production 2-stroke turbo.
The goal with any all-new powertrain project is to build a stable, high performance production 2-stroke turbo, without any compromises. Countless hours are spent designing components in CAD, flow and combustion software analysis, and building one-off prototype engines and components by hand. The team began working down a variety of paths to identify the solutions needed, exploring forced induction technologies, fueling innovations, and more. Arguably more difficult that the physical parts themselves was the control strategy and system. The unseen magic that occurs in the ECU is absolutely critical, providing the perfect mix of fuel, spark, and boost needed for every situation.


“The solution had to be stable on pump gas, with mass-produced components, operate with rock-solid consistency no matter the conditions, and make more power. It was a hell of a challenge.” — Ricky Jaeger, Powertrain Director
“For years we went down a lot of different paths trying to solve the stability problem. There wasn’t much definition or direction, as we were in completely uncharted territory. Turbo and supercharger designs, injection systems, control strategies and hardware, cylinder and exhaust work, you name it -we tried it. In some way, however, everything we explored contributed to what we have today. Whether we learned what not to do or were able to take a small learning and use it going forward, it all lead to Patriot Boost.” said Marty Sampson, Snowmobile Product Director.
The team was facing additional challenges from the corporation: if the next-level turbo wasn’t possible, there are other projects and programs that could use the funding. The snowmobile industry is built on new product innovation, but they only mattered if they eventually got in the customer’s hands. The corporation had taken the leap to invest a lot of money into the project without knowing how long it would take, or what would even come of it.
In 2015, the project team began quarterly updates and reports with the executive leadership at Polaris. There, they provided technical updates on the progress they made, what they had learned, and where they planned to go next. Through the winter of 2015 and into the 2016 season, those updates were far from sunshine and roses. The room was full of passionate snowmobilers, sure, but those same people were brilliant engineers and smart businesspeople that well understood the technical and financial challenges.

Progress was being made into 2017, with the hardware and software direction defined and moving. The turbocharger and auxiliary throttle body injectors were the path, and the controls needed were being built into the upcoming Patriot 850 ECU and electrical system. Things were improving, but the level of combustion stability needed to make the power consistently and reliably still wasn’t there.

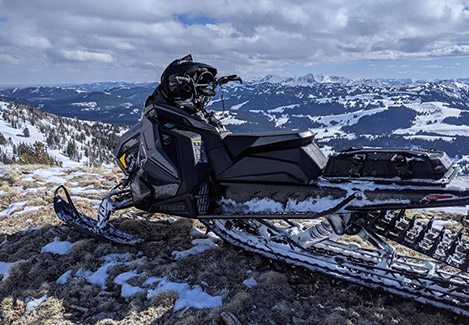
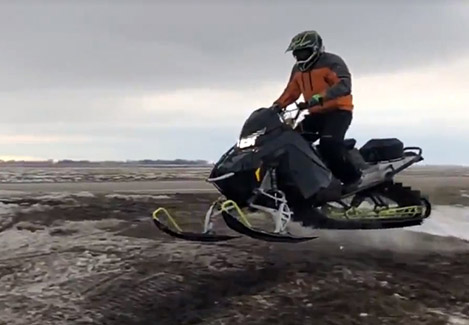
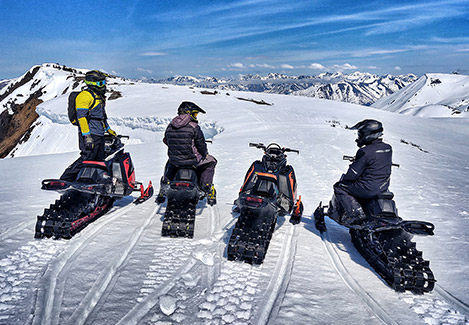
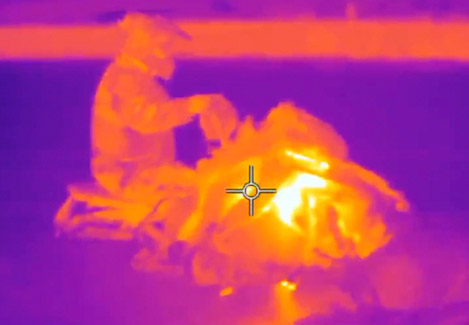
Dyno Cell #6 Ground Zero For The Future Of Turbo Performance
That fateful day in Dyno Cell #6 couldn’t have come at a better time. Jim Buchwitz and Darren Hedlund were testing another rev of their prototype Patriot turbo engine. They had been struggling with maintaining stable combustion while under higher boost levels. The exhaust flow would produce turbulent, violent air that was difficult to control as it entered the turbocharger, and the detonation limits of the 91 octane fuel in the tank weren’t helping. Every 2-stroke turbo up to that point had an internal wastegate, meaning that the wastegate valve for excess exhaust gasses to exit was located in the turbo housing itself. That meant that all of the exhaust leaving the engine made it all the way to the turbo before being used for boost or exited the wastegate.
The tuned pipe of a 2-stroke engine is specifically designed for that exact engine, and has an immense impact on the performance of the engine. The shape and size of the tuned pipe helps draw exhaust gasses out of the engine efficiently, delivering better response and power. The tuned pipe was not, however, designed to deliver smooth exhaust to a turbocharger.
The engine had shown a level of stability and control that they had been searching for. When they investigated, they began discussing a radical idea: if that is where the air wants to exit, then let it exit there. That idea would lead to Smart Boost, a divorced wastegate located right on the tuned pipe that provided the control needed while relieving the pressure in the tuned pipe. They spent the summer replicating the stability, developing the hardware, tuning the controls, and making it work.

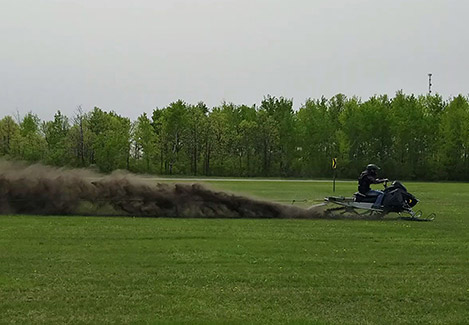
“When we saw the stability in the engine, that’s when we knew we really had something on our hands.” said Darren Hedlund, Powertrain Development Specialist.
By November of 2018, the Medusa project was brought up to a full production program, with a launch date of March 1st, 2021 circled on the calendar.
Anyone can bolt on a turbo, we built a whole new system.